[:en]
Interpolateurs
Interpolateurs
I ) Travail de la carte électronique interpolateur
L’utilisateur après avoir préparé un fichier Gcode ( séquence de déplacements de l’outil ) grâce à un ordinateur va l’envoyer vers l’électronique de commande. Cette électronique de commande est constituée par ce qu’on appelle une carte d’interpolation ou un interpolateur.
Le travail de l’interpolateur est d’interpréter les commandes Gcode pour envoyer le bon nombre d’impulsions vers les moteurs des axes de déplacement.
Dans le langage Gcode seuls les points de départ et d’arrivée sont indiqués donc l’interpolateur va devoir :
3 ) envoyer ces impulsions à une fréquence tenant compte de la vitesse de déplacement demandée ( F200 pour 200 mm/min dans notre exemple )
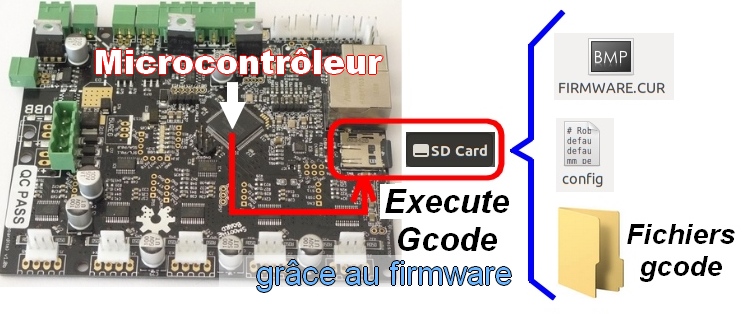
C’est pour cela que dans les documentations techniques d’une carte interpolateur on met en avant la puissance de son microcontrôleur, 32 bit, 200 MHz par exemple.
Fluid NC
Fluid NC
I ) Installation de FluidNC
1 ) Installation du firmware avec communication Wifi
Allez vers la partie Github https://github.com/bdring/FluidNC/releases
Si votre poste d’installation est windows, choisir de télécharger le fichier Zip, si votre version de windows est 64bit choisir la version win64
Si votre poste d’installation est Linux, MacOs ou Unix télécharger les sources.
Après décompression du fichier Zip, des scripts bat vont permettre de réaliser différentes installation.
Si votre ESP32 possède déjà un firmware il est préférable d’effacer la mémoire flash avec « erase.bat«
Si vous installez la version Wifi exécutez « install-wifi.bat«
Après avoir installé la version Wifi il est indispensable d’exécuter « install-fs.bat » pour installer le index.html.gz de l’interface WebUI
2 ) Installation du fichier config
Démarrez la console « fluidterm.bat«
Après avoir envoyé le fichier config yaml il faut indiquer qu’il sera utilisé par le firmware en tapant la commande $Config/Filename=<tonfichierconfig.yaml>
Ne pas oublier de redémarrer fluidnc pour que le fichier de config soit pris en compte
3 ) Ajouter la langue Française
Récupérez le fichier index.html.gz dans le sous dossier « fr » du github github.com/luc-github/ESP3D-WEBUI/tree/2.1/languages
Connectez vous ensuite à l’interface WebUI puis allez dans les paramètres ESP3D
On accède à l’interface Web soit avec l’adresse IP x.x.x.x/ ou fluidnc.local/ ou fluidnc
Comme le Webui et notamment le fichier index.html.gz est associé au firmware, cliquez sur l’icône jaune.
4 ) Installation du firmware avec communication Bluetooth
Les pilotes de moteurs PAP
Les pilotes de moteurs PAP
MKS-TMC2160-OC
Il est possible de paramétrer ce type de driver en SPI mais en ajoutant un connecteur 4 broche en connectant une résistance et en mettant tous les micro-interrupteurs à off https://github.com/makerbase-mks/MKS-Big-Current-Driver/issues/2
Les détecteurs et capteurs
Les détecteurs et capteurs
I ) Les détecteurs de fin de course
1 ) Détecteurs de fin de course mécaniques
Le câblage
Il y a deux possibilités, câbler les trois câbles Gnd (-), Vcc (+) et signal vers l’électronique de commande ce qui ne pose normalement aucune difficulté.
ou câbler seulement le signal en COM et l’alimentation – en borne NC
La quasi-totalité des électroniques de commande possèdent un dispositif qui fait qu’automatiquement lorsqu’elle ne détecte plus de 0V venant du capteur, un voltage positif arrive à sa borne. ( système électronique avec résistance de rappel ).
Le fait que un signal « 0 » arrive vers l’électronique de commande donne l’information « je suis touché, ou mon fils est cassé alors moteur d’axe arrête toi »
L’électronique de commande ne détecte plus le 0 Volt du capteur, car le capteur est activé ( situation normale )
ou parce que le câble du 0 Volt s’est cassé, détaché ou dessoudé ( panne )
Cette manière de câbler permet que quand un fil du capteur est défectueux, la machine s’arrête au lieu de continuer sans pouvoir s’arrêter.
2 ) Détecteurs inductifs
Les détecteurs inductifs détectent exclusivement les objets métalliques.
Le détecteur inductif coûte un peu plus cher que le détecteur mécanique, son avantage est qu’il n’y a pas de contact physique avec l’objet à détecter donc moins d’usure et durée de vie indépendante du nombre de détections, le détecteur est encapsulé dans une résine donc étanche et pas de risque de court circuit en cas de liquide qui coule sur la machine. Un voyant permet de visualiser la détection donc on peut voir si le détecteur est opérationnel sans faire de vérification au niveau de l’interpolateur.
Branchements des capteurs inductifs
Les détecteurs ou capteurs peuvent être équipés de sorties types PNP et NPN
Les capteurs inductifs possèdent 3 fils, généralement marron pour le +(vcc), bleu pour le – (gnd) et noir pour signal.
-
type PNP : commutation sur la charge du potentiel positif.
La charge (bobine de relais, entrée de contacteur auxiliaire, entrée automate) est à installer entre le – ( bleu ) et signal ( noir ) -
type NPN : commutation sur la charge du potentiel négatif.
La charge est a installer entre le +(vcc) marron et le signal ( noir )Attention !! pour la plupart des entrées des électroniques de commande de CNC, il faut utiliser des capteurs inductifs avec sortie NPN
Exemple de branchement de capteur inductif NPN
Motorisation des axes avec des servomoteurs
Motorisation des axes avec des servomoteurs
Le servomoteur est un moteur dont la position est vérifiée en continu et corrigée en fonction de la mesure. C’est donc un mécanisme asservi, d’où le nom de ‘servo’.
Le servomoteur est composé :
– d’un moteur qui le plus souvent est à courant continu, mais il existe également des modèles puissants alimentés en courant alternatif triphasé.
– d’un système permettant de connaître la position de l’axe de rotation (potentiomètre ou codeur)
– d’un circuit électronique permettant une régulation en boucle fermée.
Ne pas confondre !
Un servomoteur est dans le domaine de la CNC un moteur commandé de manière à effectuer des centaines de tours pour actionner une transmission destinée à parcourir une course allant de 100 à 3000 mm.
Le même terme est utilisé pour les servomoteurs de modélisme, dont la sortie se fait généralement en rotation sur un angle de l’ordre de 140°. Il s’agit aussi d’un mécanisme asservi en position, d’ou le terme de ‘servo’, mais la précision est faible, et le principe de commande très différent.
Quels avantages pour une CNC par rapport à un moteur pas-à-pas classique ?
– le servo moteur fonctionne en boucle fermée et en cas d’efforts importants ne peut pas perdre sa position
– le servo moteur peut être très précis, encore plus que le moteur pas à pas, car cela dépend de la résolution de l’encodeur pas de la constitution du moteur.
– le servo moteur garde un couple important même à haute vitesse et il est capable d’accélérations importantes.
Les inconvénients
– le prix d’achat d’un servo moteur est beaucoup plus élevé que celui d’un moteur pas à pas, de même le driver qui va piloter un servo moteur est plus cher qu’un driver de moteur PAP
– l’installation et le paramétrage est beaucoup plus complexe avec un servo moteur qu’un moteur pas à pas.
Dans quel cas le servo moteur est préféré aux moteurs pas à pas pour les fraiseuses CNC ?
Lorsqu’une précision très importante est nécessaire : la résolution d’un moteur pas à pas est limitée de par sa constitution alors que celle d’un servo moteur dépend seulement de son codeur et de l’électronique derrière capable d’exploiter les mesures.
Il est possible d’augmenter pour un moteur pas à pas les micro-pas pour augmenter la résolution, mais cela entraine proportionnellement une diminution du couple surtout à grande vitesse.
Mais une précision très importante autour du 1/100 de mm voir plus n’est pas nécessaire dans la majorité des cas et une grande résolution dans l’entrainement des déplacements est exploité seulement lorsque
l’ensemble mécanique de la machine est adapté pour la grande précision.
Lorsque de longs déplacements d’axe doivent s’effectuer à grande vitesse avec des accélérations importantes : il est clair que ces déplacements se font outils hors matière d’un usinage à un autre, à l’intérieur de la matière, la vitesse est de toute façon limitée par la résistance de l’outil. On est la dans des préoccupations de productivité, gagner quelques minutes pour chaque pièce afin de gagner suffisamment pour justifier l’investissement au bout de quelques années, lorsque la machine est utilisée pour de la série toute la journée.
Lorsqu’il y a plusieurs pièces à usiner dans une grande plaque, l’investissement dans un logiciel d’imbrication (nesting) permet d’optimiser l’ordre des usinages et limiter les déplacements d’outil.
Si les déplacements hors usinage ne sont pas trop longs, le gain de productivité entre les servo moteur et les moteurs pas à pas avec codeur de forte puissance ne sera pas important.
Principe de l’asservissement
Le principe de base de l’asservissement est de mesurer, en permanence, l’écart entre la valeur réelle mesurée du processus asservi et la valeur de consigne que l’on désire atteindre, puis de calculer la commande appropriée à appliquer à un (ou des) actionneur(s) de façon à réduire cet écart le plus rapidement possible.
Pour l’asservissement, la consigne évolue en permanence, ce qui n’est pas le cas de la régulation ou la consigne reste stable (exemple d’une régulation de chauffage)
A ) Qualités de l’asservissement
La précision
C’est la capacité du système à se rapprocher le plus possible de la valeur de consigne.
La rapidité
C’est la capacité du système à atteindre dans les meilleurs délais son régime stable.
La stabilité
C’est la capacité du système à se rapprocher de la consigne avec le minimum d’oscillation.
Le taux de dépassement caractérise l’amplitude maximale des oscillations.
B ) Les correcteurs
Un correcteur est un algorithme de calcul qui délivre un signal de commande à partir de la
différence entre la consigne et la mesure.
Le correcteur PID agit de 3 manières :
Action Proportionnelle : l’erreur est multipliée par un gain G appelé aussi Kp
Action Intégrale : l’erreur est intégrée et divisée par un gain Ti appelé aussi Ki
Action Dérivée : l’erreur est dérivée et multipliée par un gain Td appelé aussi Kd
Pour ces trois paramètres, le réglage au-delà d’un seuil trop élevé a pour effet d’engendrer une oscillation du système de plus en plus importante menant à l’instabilité.
L’analyse du système avec un PID est très simple, mais sa conception peut être délicate, voire difficile, car il n’existe pas de méthode unique pour résoudre ce problème.
Il faut trouver des compromis, le régulateur idéal n’existe pas
L’action proportionnelle : lorsque P augmente, le temps de montée (rise time) est plus court, mais il y a un dépassement plus important. Le temps d’établissement varie peu et l’erreur statique se trouve améliorée.
L’action intégrale : Lorsque 1/Ti augmente, le temps de montée est plus court, mais il y a un dépassement plus important.
Le temps d’établissement au régime stationnaire s’allonge, mais dans ce cas on assure une erreur statique nulle.
Donc plus ce paramètre est élevé, plus la réponse du système est ralentie.
L’action dérivée : lorsqu’augmenté, le temps de montée change peu, mais le dépassement diminue.
Le temps d’établissement au régime stationnaire est meilleur. Pas d’influences sur l’erreur statique.
Si ce paramètre est trop élevé dans un premier temps il stabilise le système en le ralentissant trop, mais dans un deuxième temps le régulateur anticipe trop
et un système à temps mort élevé devient rapidement instable.
Simulateur PID en ligne : http://www.olliw.eu/storm32bgc-wiki/PID_online_simulator
Un facteur externe a l’électronique de commande et aux servo moteur car dépendant de la structure mécanique de chaque machine est celui de l’inertie.
Trouver la bonne formule de PID en précision, stabilité et rapidité en fonction de l’inertie est très délicat à régler manuellement.
Les servo moteurs ont des liaisons série ( modbus, CAN, Ethernet … ) permettant de les paramétrer via un logiciel, ils ont généralement un mode auto-tuning (auto-réglage).
Libre à vous de modifier ensuite les gains manuellement si vous les désirez.
Ci-dessous un exemple d’écran auto-tuning d’un logiciel de paramétrage servo
Certains servo moteurs possèdent un frein, cela permet de maintenir une position lorsque l’électricité est coupée, très utile notamment pour l’axe Z lorsque l’électricité est coupée.
Motorisation des axes avec des moteur pas à pas
Motorisation des axes avec des moteur pas à pas
Le moteur pas à pas fut inventé en 1936 par Marius Lavet, un ingénieur français des Arts et Métiers, pour l’industrie horlogère (source Wikipédia)
I ) Fonctionnement
Le moteur pas-à-pas possède un rotor avec un aimant permanent et un stator avec deux bobines A et B, le courant traverse ces bobines dans un sens puis ensuite dans l’autre inversant ainsi les polarités.
L’extérieur du rotor ainsi que les noyaux des bobines du stator ont des dents.
La construction est réalisée pour que lorsque les dents de la bobine A aimantent les dents du pôle opposé du rotor, les dents de la bobine B ne soient en face d’aucune dent du rotor.
Ainsi lorsque c’est la bobine B qui est alimentée a son tour, le rotor fait une légère rotation, l’aimantation alignant ces autres dents.
Les possibilités de déplacement angulaire
sont nombreuses, selon le sens de déplacement du courant dans les bobines,
on attire différentes dents du rotor (dents rouges ou bleus dans cette animation)
Il y a beaucoup de types de moteurs, pas à pas.
Ceux utilisés par les machines CNC sont précisément des moteurs pas-à-pas hybrides bipolaires.
Si vous démontez un moteur pas à pas vous verrez 8 enroulements dans le stator, même s’il y a bien que deux bobines en deux parties réparties sur tout le pourtour.
Il y a d’ailleurs 4 fils correspondant aux 2 extrémités d’une bobine plus 2 extrémités de l’autre bobine.
Remarques : ne démontez pas des moteurs pas-à-pas que vous comptez utiliser, après démontage, la qualité des aimants permanents à l’intérieur est diminuée et le moteur sera moins performant après remontage.
II ) Normes et caractéristiques
La norme Nema correspond à des dimensions utiles pour la fixation du moteur dans une machine.
Ce qui permet l’interopérabilité puisqu’un moteur Nema 23 d’un fabricant peut être remplacé par un autre moteur nema 23 de mêmes caractéristiques d’un autre fabricant.
Contrairement à ce que beaucoup pensent, Nema n’indique rien sur la puissance du moteur, il est vrai que plus un moteur est gros plus il y a de chance qu’il soit puissant, mais la taille c’est aussi la longueur du moteur. Et un moteur Nema 17 long peut être plus puissant qu’un Nema 23 très court.
Les moteurs pas-à-pas plus longs ont des bobines de stators plus importantes, les rotors ont le double d’aimants permanents 4 au lieu de 2, ce qui augmente la puissance.
Ce qui compte dans un moteur pas à pas c’est le couple en N. m, c’est indiqué sur les fiches techniques du fabricant.
Le couple disponible peut être différent selon la vitesse de rotation du moteur et l’intensité du courant envoyé dans ses bobines.
Le couple indiqué par le fabricant est celui du « couple d’arrêts », le couple maxi à partir du moment où on fait sauter un pas le moteur à l’arrêt.
Le couple ensuite diminue en fonction de la vitesse, un moteur pas à pas est plus performant à faible vitesse qu’à vitesse importante.
Le couple possible sans perte de pas est plus faible au moment du démarrage qu’en vitesse de travail, c’est pour cela que pour le pilotage des moteurs pas à pas il faut paramétrer des phases d’accélération et décélérations.
Il est évident que plus un moteur est gros, plus ses bobinages pourront supporter une intensité importante et plus il pourra maintenir un couple important à haute vitesse.
Mais pour un même moteur plus on l’alimente avec un voltage important, plus il gardera du couple à grande vitesse, il est également évident que les moteurs de plus grande taille acceptent des voltages plus élevés que les petits. Dans les données constructeur il y a une plage pour alimenter les moteurs pas à pas, par exemple 12V à 50V, choisissez toujours la partie haute de la plage par exemple une alimentation électrique de 36V au lieu de 24V ou mieux 48 V.
Le moteur pas-à-pas bipolaire classique permet de faire 200 pas en un tour c’est-à-dire à chaque fois des déplacements angulaires de 1,8 deg
On peut trouver également des moteurs PAP de 400 pas / tours avec des déplacements angulaires de 0,9 deg
III ) Branchements
Les pilotes de moteurs pas-à-pas ont un bornier où doivent être branchés les 4 fils du moteur.
Cet emplacement est noté A+ A – (une bobine du moteur) et B+ B – (l’autre bobine du moteur)
Souvent les moteurs bipolaires ont comme couleur de fils rouge, bleu, vert, noir correspondant à A+ A — B+ B-
Sinon cela peut être marron, orange, rouge et jaune pour A+ A — B+ B —
Mais vous pouvez très bien tomber sur un code de couleur de fils plus exotique, il donc nécessaire de connaître la méthode ci-dessous qui consiste a tester les bobines avec un testeur de continuité.
Pour brancher correctement les fils, il faut faire un test de continuité entre ceux-ci pour voir s’ils appartiennent à la même bobine ou pas.
Si vous identifiez une bobine, car les deux fils font sonner le testeur de continuité appelez la B ou A cela n’a pas d’importante, si vous l’appelez arbitrairement, A l’autre s’appellera B.
Maintenant que l’une des bobines a été nommée A lequel fil de la bobine est A+ lequel est A — ? cela n’a pas beaucoup d’importance non plus, si les fils sont inversés le moteur tournera à l’envers.
Pour faire tourner un moteur pas à pas dans l’autre sens, il faut inverser le branchement des fils d’une seule bobine, ou changer un paramètre dans l’électronique de commande pour faire une inversion logicielle.
Vous saurez si le moteur tourne à l’endroit ou à l’envers quand vous ferez vos premiers tests de déplacement des axes de la machine.
Motorisation de la broche
Motorisation de la broche
La fonction d’une broche de machine outil est d’assurer un guidage précis en rotation de l’outil.
Cet outil est inséré dans un porte outil, la broche pour assurer le guidage en rotation possède des roulements.
I ) Motorisation de la broche
Pour certaines machines l’entrainement de la broche est assuré par un moteur grâce à une courroie.
Comme dans l’exemple ci-dessous pour une fraiseuse verticale.
Dans d’autre cas plus rares le moteur entraine directement la broche en bout avec un accouplement.
Pour une machine-outil il est essentiel d’avoir un réglage de vitesse de broche, les moteurs asynchrones devront donc avoir un variateur, par exemple un variateur par changement de fréquence.
Remarque :
Concernant les solutions de motorisation ci-dessus, l’ensemble pèse lourd.
Cela ne gène pas pour les fraiseuses verticales ( tête fixe ou déplacement seulement en Z ) mais pose problème pour les fraiseuses à portique.
Pour les fraiseuses à portique, on va privilégier les électrobroches ( motorisation et guidage compact dans un même ensemble ) ou les broches VFD ( variation de fréquence )
II ) Les électrobroches
Cette fois le guidage et l’entrainement en rotation sont regroupé dans un même matériel.
Le moteurs électrique universel, c’est le type de moteur qu’on trouve partout dans le matériel électroportatif, les appareils électroménager …
Le moteur électrique universel à beaucoup d’éléments communs avec le moteur à courant continu, notamment un collecteur et des balais.
Par contre même si dans la pratique on branche ce type de moteur sur une prise électrique secteur, donc 220V monophasé, on peut faire fonctionner indifféremment le moteur universel en continu ou alternatif.
Le moteur universel est très utilisé pour les puissances faibles à moyenne, il est économique à construire et à un bon couple au démarrage.
Par contre son principal inconvénient est qu’il nécessite un changement de balais au bout d’un certain temps à cause du frottement sur le collecteur.
Les étincelles entre les balais et le collecteur peuvent provoquer des perturbations électromagnétiques.
Les moteurs de fraisage doivent avoir des protections contre ces perturbations qui pourrait provoquer des déconnexions dans l’électronique de pilotage.
A ) Electrobroche avec moteur universel d’entrée de gamme
Il est possible d’adapter à des fraiseuses CNC des électrobroches prévus au départ pour des défonceuses.
Comme pour les modèles ci-dessus (Makita RT0701C, Bosh Colt et Dewalt DWP611 ) qui sont assez souvent utilisés pour le fraisages avec des petites fraiseuses Hobbyistes.
Ces défonceuses ont en général une puissance de 800W, elles sont plus bruyantes que les broches dédiés au fraisage et il est préférable de les réserver à l’usinage du bois et matières plastiques. Les roulements supporteraient mal des usinages réguliers et prolongés par exemple dans l’aluminium.
B ) Electrobroche avec moteur universel de milieu de gamme.
Ces électrobroches sont construites spécifiquement pour l’usinage. Elle peuvent usiner le bois les matières plastiques et les métaux tendres ( aluminium, cuivre, laiton … )
La puissance va de 800W à 1050W et des options sont possibles pour avoir
– un système de changement automatique d’outils ATC ( Automatic Change Tools )
– un pilotage de la vitesse à partir de l’électronique de commande
Les broches de marque Allemande Kress rachetés récemment par une autre marque Allemande AMB sont très connus et équipent beaucoup de fraiseuses CNC.
Ont trouve également dans la même gamme la marque Allemande Mafell.
C ) Electrobroches avec moteur universel puissantes
Les électrobroches Suisse Suhner peuvent aller jusqu’a une puissance de 1800 Watt.
Les porte outils sont identiques et compatibles avec les broches Kress AMD et Mafell
Le même système de changement automatique d’outil que les broches Kress peut être utilisé.
Mais contrairement au moteur à courant continu classique, la partie bobinée ( inducteur ) est fixe.
Cette partie fixe bobinée est alimentée par un circuit électronique de commande qui va activer successivement les bobines, ont a donc plus les inconvénients du collecteur et des balais.
Ce sont des petits capteurs à effet Hall qui vont donner l’information à l’électronique pour commuter au bon moment.
Ci dessous le principe de fonctionnement
Les marques de matériel électroportatif sur batterie, passent progressivement du moteur électrique universel au moteur brushless.
II ) Branchement des électrobroche avec variateur de fréquence
Les prises XLR Aviation des électrobroches ont les connecteurs numérotés de 1 à 4
Il est important de relier la broche 4 à la terre. Pour les broches 123 une inversion va juste faire tourner la broche à l’envers.
III ) Exemple de l’inverter VFD Huanyang HY01D523B
Les inverteurs de l’entreprise Hongkongaise Huanyang sont bon marchés et très répandus, le modèle HY01D523B à une puissance de 1.5Kw.
Il est important que la carcasse de la broche soit reliée à la terre, généralement elle est reliée à terre par l’intermédiaire du support de broche lorsque la machine elle même est reliée à la terre.
Pour un pilotage manuel de la broche seul le bornier inférieur est utilisé, les borniers verts supérieurs sont à relier à un panneau de commande ou l’interpolateur de pilotage.
Paramétrage de l’inverter VFD Huanyang HY01D523B
A faire dans cet ordre
Pd013 —-> réinitialisation de l’appareil mettre 1 ( paramètre 8 sur certains modèles plus anciens )
Pd005 —-> fréquence maximale, entrer 400 (soit 24000 rpm)
Pd004 —–> fréquence nominale du moteur, entrer 400
Pd003 —–> fréquence de démarrage, c’est à dire fréquence à laquelle le moteur va se lancer lors du démarrage avec le bouton run.
mettre par exemple 200, soit 12000 tours…
Pd011 ——> fréquence minimale. Par exemple 50 soit 3000 tours : en dessous le moteur à trop peu de couple pour usiner… Par contre si on veux se servir d’une pinule, il est possible de choisir encore plus lent.
Pd014 —> temps pour accélérer, en secondes, sur une 1kw5 normalement 2 secondes suffisent
Pd015 —-> temps pour s’arrêter (on ne se servira pas de la fonction de freinage qui abime le matériel, ici comme on est pas pressé on va laisser la broche s’arrêter en douceur, et on rentre 2 ou 3 secondes également)
Pd023 —-> Si 1 le moteur peut tourner dans 2 sens / si 0 le moteur tourne dans un seul sens
Pd144 —-> vitesse du moteur à 50hz, entrer 3000 au lieu de 1440 (ceci ne change pas le comportement du variateur, c’est juste pour avoir un affichage de la vitesse qui correspond à la réalité)
Pd145 —-> le variateur va augmenter la tension s’il détecte que le moteur peine. Ce paramètre peut être réglé de 1 à 10. Attention: plus c’est haut, plus le moteur risque de chauffer en cas d’effort important. On peut rentrer 6 par exemple pour ne pas faire trop chauffer le moteur.
III ) Les broches dont la vitesse de rotation varie avec la fréquence
Les moteurs triphasés asynchrones sont prévus pour tourner à 3000 tr/min avec 50 Hz (fréquence du réseau électrique français)
Si on transporte les mêmes moteurs aux États-Unis, ils tourneront à 3600 tr/min avec 60 Hz
La vitesse du moteur triphasé asynchrone dépend de la fréquence d’alimentation de ses bobines.
Le principe est donc de lisser le signal alternatif du réseau électrique (courant continu) puis avec une électronique de puissance, recréer un signal alternatif dont la fréquence cette fois-ci peut varier selon le choix de l’utilisateur.
Ce type de variateur peut être utilisé pour faire varier n’importe quel moteur asynchrone triphasé 220 ou 380 V même si chez vous, vous n’avez que du 220 V ou 240 V mono.
Ceci est très pratique pour faire fonctionner une machine en 380V triphasé lorsque l’on dispose que d’un réseau 220V monophasé.
Il existe également des variateurs VFD triphasé —-> triphasé
La liaison entre le variateur et la broche doit se faire via un câble blindé, la connexion se fait avec un connecteur XLR type aviation
Les trois phases UVW se branchent respectivement sur les broches 123 du connecteur XLR.
La terre n’est pas toujours connectée à la broche N° 4, s’il y a un défaut d’isolement dans la broche au niveau de sa carcasse, l’électricité pourra toujours partir vers la terre de la machine via le support de broche, il est donc important de mettre le chassis de la machine à la terre.
La motorisation
Les systèmes d’entrainement
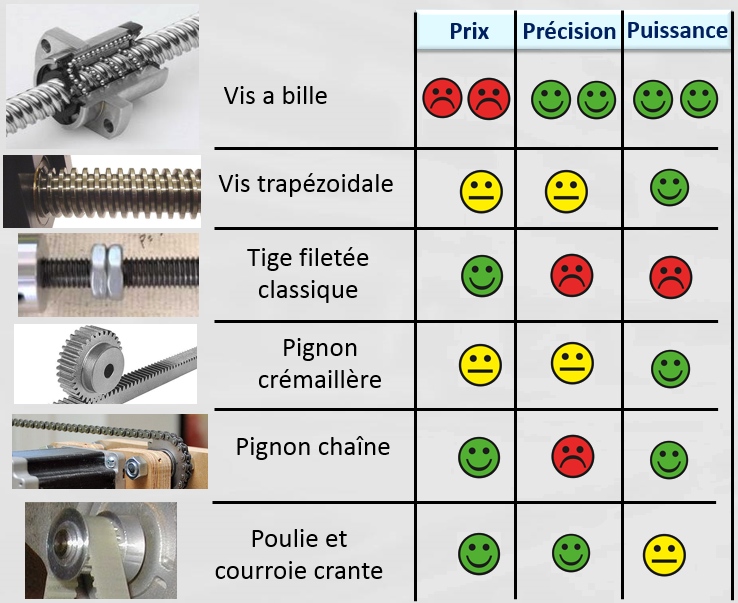
Système d’entrainement par pignon crémaillère
Avantages :
- Permet des vitesses de déplacement et accélérations importantes
- Peut transmettre des charges importantes sur de longues distances
- Moins cher que les vis à billes en particulier sur les longues distances
- Garde la mêmes précision quel que soit la distance de déplacement
Inconvénients :
- Nécessite un système permettant d’annuler les jeux dans le cas des pignons à denture droite.
Il est préférable pour limiter les jeux de fonctionnement d’utiliser des crémaillères et pignons à dentures hélicoïdales. - Ce système reste cependant moins précis que les vis à bille mais comme les machines de grande taille ne sont pas faites pour usiner le micron la précision reste suffisante.
Système d’entrainement par courroies crantées
Avantages :
- Permet des vitesses de déplacement et accélérations importantes
- Grande précision et pas de jeux de fonctionnement
- Solution très économique
- Fonctionnement silencieux
Inconvénients :
- Ne permet pas de transmettre des efforts aussi important qu’avec une vis à bille
- Perd en précision (allongement) sur des longues distances contrairement aux crémaillères.
Remarques : ces inconvénients peuvent être réduis en choisissant des courroies crantées renforcées avec fil d’acier, un système avec courroies crantés qui s’engrène avec une autre cette fois fixe permet également de supprimer l’allongement sur les grandes distances mais le système est très difficile à mettre en oeuvre.
Les systèmes d’entrainement
Le choix du système de transmission pour une CNC dépend de beaucoup de paramètres
– du budget
– de la précision requise
– du couple à transmettre
– des vitesses et accélération de déplacement
Le système doit également être cohérent avec les reste de la machine, pas la peine de choisir une transmission très chère et ultra précise si le châssis de la machine n’est pas suffisamment rigide.
Remarques :
Les transmissions par chaines ou vis écrous classiques ne sont pas détaillés ici car ils présentent trop d’inconvénients pour la construction de fraiseuses CNC.
La transmission ne doit pas être considérée seule, les avantages et inconvénients d’une solution peuvent être modulés en fonction de la rigidité de la machine, de la motorisation utilisée.
Système d’entrainement par vis à billes
Avantages :
Très grande précision, pas de jeux, pas de frottements dans la transmission
Inconvénients :
Prix en particulier lors des grandes longueurs.
Ne conviens pas aux transmissions de très grandes longueurs, risque de flambage lorsque la vitesse de rotation augmente et dans ce cas il est préférable d’entrainer en rotation l’écrou plutôt que la vis.
Remarques : des nouvelles techniques de fabrication ont réduit le prix des vis à billes, il y a plusieurs niveaux de précision dans les vis à billes donc différents prix.
Système d’entrainement par vis écrous à profil trapézoidal ou carré.
Avantages :
- Permet de transmettre des efforts importants
- Solution plus économique que les vis à bille
Inconvénients :
IL y a beaucoup de jeu entre la vis et l’écrou qu’il faut compenser pour l’éliminer avec un ressort (ce n’est pas une solution idéale)
Ces vis trapézoïdales sont utilisées habituellement pour des déplacements avec des efforts importants sans nécessiter de précisions.
Les vis à filet trapézoïdal ou carré ne sont pas adaptées aux déplacements d’axe pour la plupart des machines CNC,
à cause du jeu et donc du manque de précision lorsque les déplacements changent de direction.
On trouve cependant ce type de transmission pour de petites fraiseuses CNC bon marché pour des raisons de coûts.
Structure d’une CNC
[:fr]
Structure d’une CNC
Sur le web
Protocase https://www.protocase.com/
Entreprise Canadienne de création de carters, boitiers métalliques pour prototypage.
Logiciel Protocase Designer pour créer sa forme en tôle et directement un devis
Les options et accessoires
Les options et accessoires
du stratifié carbone sans faire de poussière, de la pièrre, du marbre …
Concernant le modèle ci-dessus, la table en aluminium rainuré à une surface de bridage de 345 x 305mm
Le système rend l’usinage plus silencieux et grâce à la pompe de transfert intégré, le liquide peut être rapidement évacué après l’usinage de la pièce.
Le liquide de refroidissement est à base de Glycol, bien connu dans l’industrie automobile pour ses propriétés réfrigérantes et non corrosives.
En Anglais A.T.C ( Automatic Tool Changer )
Les systèmes de guidage
Les systèmes de guidage
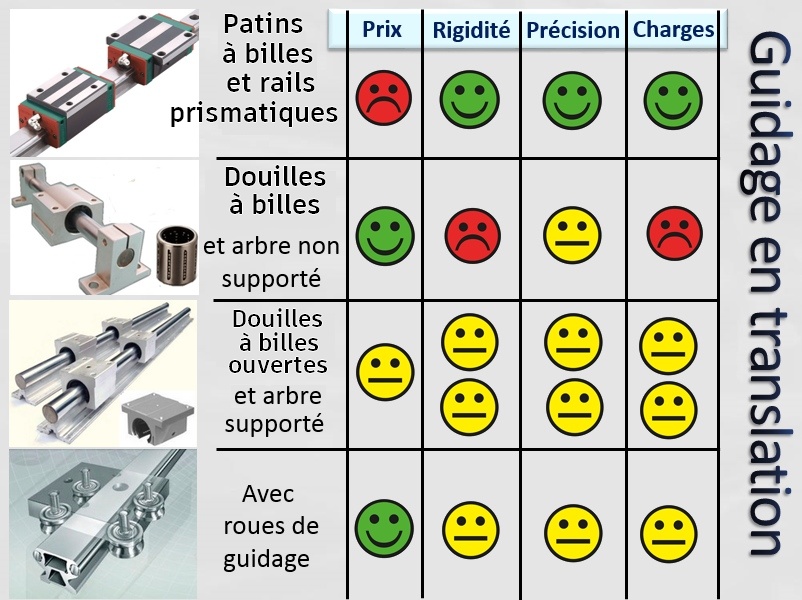
Le choix du système de guidage en translation pour une CNC dépend de beaucoup de paramètres.
– du budget
– de la précision requise
– des efforts à supporter
– de la structure de la machine
Le système de guidage doit être normalement cohérent avec le reste de la machine et un type de guidage correspond généralement à un type de châssis.
Vous avez ci-dessous un contre exemple avec une fraiseuse 6040 qu’on peut trouver commercialisée avec trois types de guidages, bien que la rigidité de la structure est pratiquement identique dans les trois cas.
La raison est économique, des rails prismatique coûtent plus cher que des rails cylindriques.
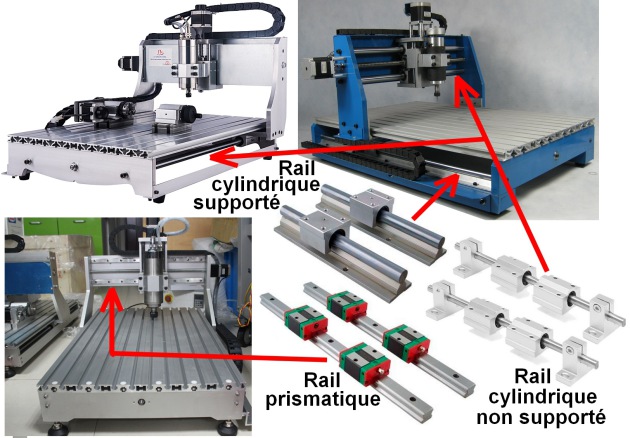
Si votre machine possède des rails assez long non supportés, il est impossible d’usiner des matières dures telles que bois massif et aluminium, d’importantes vibrations se feront au niveau du rail.
Les rails supportés peuvent être cylindriques ou prismatiques, le choix entre les deux doit se faire en fonction :
– de la sollicitation de la machine, si vous utiliser la machine toute la journée avec des cadences industrielles, les rails prismatiques en général vont être moins usés que les cylindriques au bout de plusieurs dizaines d’années.
– de la précision recherchée, les patins prismatiques peuvent être pré-contrains, donc absence totale de jeux de fonctionnement. Mais si le reste de la machine fait que vous avez des pertes de précision ailleurs, rails cylindriques ou prismatiques vous ne verrez pas la différence au niveau précision, surtout si c’est pour usiner du bois.
– de la charge à supporter, si vous avez un portique de machine très lourd, les guidages cylindriques se font que sur une seule rangée de bille alors que pour les patins prismatiques cela peut être sur plusieurs rangées.
Les axes d’une fraiseuse CNC
Les axes d’une fraiseuse CNC
Fraiseuse 3 axes
Les 3 axes sont les axes de translation nommés XYZ
L’axe de la broche Z n’est pas forcément perpendiculaire à la table
Dans le cas des machines à banc fixe ( la table se déplace ) on trouve des fraiseuses verticales et horizontales.
Pour les fraiseuses verticales : l’axe de la broche est perpendiculaire à la table
Pour les fraiseuses horizontales : l’axe de la broche est parallèle à la table
Exemple des fraiseuses CNC Formosa
Les fraiseuses Formosa sont des fraiseuses à portique et pour ce type de machine l’axe Z est perpendiculaire à la table.
Remarque : il existe une convention dans le monde industriel ou l’axe X est plutôt celui du plus grand déplacement.
Cette convention n’est pas forcément respectée pour les machines autoconstruites.
De façon que quelle que soit la taille de la machine l’interface logicielle soit la même.
La majorité des fraiseuses à commande numérique sont des machines 3 axes.
Ce qu’il est possible de faire avec une fraiseuse 3 axes |
Ce qu’il est impossible de faire avec une fraiseuse 3 axes |
|
|
Les fraiseuses permettant l’usinage multi-axes
On parle d’usinage multi-axes quand la machines dispose d’au moins 4 axes de mouvement. En général, les machines multi-axes ont des axes XYZ pour effectuer des mouvements de translation, ainsi qu’un ou plusieurs axes capables d’effectuer des rotations.
L’ajout d’axes supplémentaires ouvre la possibilité de réaliser des usinages compliqués et impossibles à faire avec des machines 3 axes en translation ; cependant les machines multi-axes sont également plus chères, et plus complexes à utiliser.
Le nombre d’axes peut aller de 4 à plus de 10, et bien entendu plus la machine dispose d’axes plus son prix est élevé.
Fraiseuse 4 axes
En général, une fraiseuse 4 axes est tout simplement une fraiseuse 3 axes dotée d’un plateau tournant (le plus souvent parallèle à l’axe X ou Y de la machine).
C’est sur ce plateau tournant que va être fixée la matière à usiner, l’outil de coupe peut ainsi travailler sur toutes les faces parallèles à l’axe de rotation sans que l’opérateur doive intervenir pour retourner la matière le 4ème axe se charge de cela au fur et à mesure selon les commandes du programme.
Le 4ème axe est utilisé soit en mode « indexation », soit en mode « continu ».
En mode indexation, la broche avec la fraise est désactivée et aucune coupe n’est faite jusqu’à ce que l’axe 4 achève son mouvement de rotation.
En mode continu par contre, l’outil de coupe travaille en même temps que l’axe 4 tourne.
Le mode continu permet de faire des sculptures sur des objets cylindriques, des torsades ect …
Fraiseuse 5 axes
On peut trouver sous cette catégorie plusieurs topologies de construction.
Une fraiseuse 5 axes comporte toujours 3 axes linéaires (X, Y, Z) et 2 axes rotatifs à choisir parmi A, B et C.
Les machines vont se différencier par la position des axes rotatifs.
On trouve principalement 2 types de fraiseuse 5 axes :
2 axes rotatifs sur tête (souvent axes rotatifs B et C )
Avantage des axes rotatifs sur tête : permet d’usiner sur 3 plans sans démontage, des pièces volumineuses ou lourdes
Inconvénient : moins de rigidité et de puissance que pour des axes rotatifs sur table
Dans le domaine des fraiseuses 5 axes non industriels on trouve par exemple la fraiseuse 5 axismaker.
Interpolateurs
Interpolateurs
I ) Travail de la carte électronique interpolateur
L’utilisateur après avoir préparé un fichier Gcode ( séquence de déplacements de l’outil ) grâce à un ordinateur va l’envoyer vers l’électronique de commande. Cette électronique de commande est constituée par ce qu’on appelle une carte d’interpolation ou un interpolateur.
Le travail de l’interpolateur est d’interpréter les commandes Gcode pour envoyer le bon nombre d’impulsions vers les moteurs des axes de déplacement.
Dans le langage Gcode seuls les points de départ et d’arrivée sont indiqués donc l’interpolateur va devoir :
3 ) envoyer ces impulsions à une fréquence tenant compte de la vitesse de déplacement demandée ( F200 pour 200 mm/min dans notre exemple )
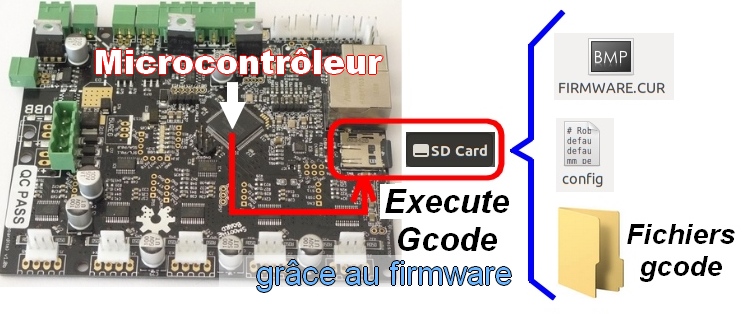
C’est pour cela que dans les documentations techniques d’une carte interpolateur on met en avant la puissance de son microcontrôleur, 32 bit, 200 MHz par exemple.
Fluid NC
Fluid NC
I ) Installation de FluidNC
1 ) Installation du firmware avec communication Wifi
Allez vers la partie Github https://github.com/bdring/FluidNC/releases
Si votre poste d’installation est windows, choisir de télécharger le fichier Zip, si votre version de windows est 64bit choisir la version win64
Si votre poste d’installation est Linux, MacOs ou Unix télécharger les sources.
Après décompression du fichier Zip, des scripts bat vont permettre de réaliser différentes installation.
Si votre ESP32 possède déjà un firmware il est préférable d’effacer la mémoire flash avec « erase.bat«
Si vous installez la version Wifi exécutez « install-wifi.bat«
Après avoir installé la version Wifi il est indispensable d’exécuter « install-fs.bat » pour installer le index.html.gz de l’interface WebUI
2 ) Installation du fichier config
Démarrez la console « fluidterm.bat«
Après avoir envoyé le fichier config yaml il faut indiquer qu’il sera utilisé par le firmware en tapant la commande $Config/Filename=<tonfichierconfig.yaml>
Ne pas oublier de redémarrer fluidnc pour que le fichier de config soit pris en compte
3 ) Ajouter la langue Française
Récupérez le fichier index.html.gz dans le sous dossier « fr » du github github.com/luc-github/ESP3D-WEBUI/tree/2.1/languages
Connectez vous ensuite à l’interface WebUI puis allez dans les paramètres ESP3D
On accède à l’interface Web soit avec l’adresse IP x.x.x.x/ ou fluidnc.local/ ou fluidnc
Comme le Webui et notamment le fichier index.html.gz est associé au firmware, cliquez sur l’icône jaune.
4 ) Installation du firmware avec communication Bluetooth
Les pilotes de moteurs PAP
Les pilotes de moteurs PAP
MKS-TMC2160-OC
Il est possible de paramétrer ce type de driver en SPI mais en ajoutant un connecteur 4 broche en connectant une résistance et en mettant tous les micro-interrupteurs à off https://github.com/makerbase-mks/MKS-Big-Current-Driver/issues/2
Les détecteurs et capteurs
Les détecteurs et capteurs
I ) Les détecteurs de fin de course
1 ) Détecteurs de fin de course mécaniques
Le câblage
Il y a deux possibilités, câbler les trois câbles Gnd (-), Vcc (+) et signal vers l’électronique de commande ce qui ne pose normalement aucune difficulté.
ou câbler seulement le signal en COM et l’alimentation – en borne NC
La quasi-totalité des électroniques de commande possèdent un dispositif qui fait qu’automatiquement lorsqu’elle ne détecte plus de 0V venant du capteur, un voltage positif arrive à sa borne. ( système électronique avec résistance de rappel ).
Le fait que un signal « 0 » arrive vers l’électronique de commande donne l’information « je suis touché, ou mon fils est cassé alors moteur d’axe arrête toi »
L’électronique de commande ne détecte plus le 0 Volt du capteur, car le capteur est activé ( situation normale )
ou parce que le câble du 0 Volt s’est cassé, détaché ou dessoudé ( panne )
Cette manière de câbler permet que quand un fil du capteur est défectueux, la machine s’arrête au lieu de continuer sans pouvoir s’arrêter.
2 ) Détecteurs inductifs
Les détecteurs inductifs détectent exclusivement les objets métalliques.
Le détecteur inductif coûte un peu plus cher que le détecteur mécanique, son avantage est qu’il n’y a pas de contact physique avec l’objet à détecter donc moins d’usure et durée de vie indépendante du nombre de détections, le détecteur est encapsulé dans une résine donc étanche et pas de risque de court circuit en cas de liquide qui coule sur la machine. Un voyant permet de visualiser la détection donc on peut voir si le détecteur est opérationnel sans faire de vérification au niveau de l’interpolateur.
Branchements des capteurs inductifs
Les détecteurs ou capteurs peuvent être équipés de sorties types PNP et NPN
Les capteurs inductifs possèdent 3 fils, généralement marron pour le +(vcc), bleu pour le – (gnd) et noir pour signal.
-
type PNP : commutation sur la charge du potentiel positif.
La charge (bobine de relais, entrée de contacteur auxiliaire, entrée automate) est à installer entre le – ( bleu ) et signal ( noir ) -
type NPN : commutation sur la charge du potentiel négatif.
La charge est a installer entre le +(vcc) marron et le signal ( noir )Attention !! pour la plupart des entrées des électroniques de commande de CNC, il faut utiliser des capteurs inductifs avec sortie NPN
Exemple de branchement de capteur inductif NPN
Motorisation des axes avec des servomoteurs
Motorisation des axes avec des servomoteurs
Le servomoteur est un moteur dont la position est vérifiée en continu et corrigée en fonction de la mesure. C’est donc un mécanisme asservi, d’où le nom de ‘servo’.
Le servomoteur est composé :
– d’un moteur qui le plus souvent est à courant continu, mais il existe également des modèles puissants alimentés en courant alternatif triphasé.
– d’un système permettant de connaître la position de l’axe de rotation (potentiomètre ou codeur)
– d’un circuit électronique permettant une régulation en boucle fermée.
Ne pas confondre !
Un servomoteur est dans le domaine de la CNC un moteur commandé de manière à effectuer des centaines de tours pour actionner une transmission destinée à parcourir une course allant de 100 à 3000 mm.
Le même terme est utilisé pour les servomoteurs de modélisme, dont la sortie se fait généralement en rotation sur un angle de l’ordre de 140°. Il s’agit aussi d’un mécanisme asservi en position, d’ou le terme de ‘servo’, mais la précision est faible, et le principe de commande très différent.
Quels avantages pour une CNC par rapport à un moteur pas-à-pas classique ?
– le servo moteur fonctionne en boucle fermée et en cas d’efforts importants ne peut pas perdre sa position
– le servo moteur peut être très précis, encore plus que le moteur pas à pas, car cela dépend de la résolution de l’encodeur pas de la constitution du moteur.
– le servo moteur garde un couple important même à haute vitesse et il est capable d’accélérations importantes.
Les inconvénients
– le prix d’achat d’un servo moteur est beaucoup plus élevé que celui d’un moteur pas à pas, de même le driver qui va piloter un servo moteur est plus cher qu’un driver de moteur PAP
– l’installation et le paramétrage est beaucoup plus complexe avec un servo moteur qu’un moteur pas à pas.
Dans quel cas le servo moteur est préféré aux moteurs pas à pas pour les fraiseuses CNC ?
Lorsqu’une précision très importante est nécessaire : la résolution d’un moteur pas à pas est limitée de par sa constitution alors que celle d’un servo moteur dépend seulement de son codeur et de l’électronique derrière capable d’exploiter les mesures.
Il est possible d’augmenter pour un moteur pas à pas les micro-pas pour augmenter la résolution, mais cela entraine proportionnellement une diminution du couple surtout à grande vitesse.
Mais une précision très importante autour du 1/100 de mm voir plus n’est pas nécessaire dans la majorité des cas et une grande résolution dans l’entrainement des déplacements est exploité seulement lorsque
l’ensemble mécanique de la machine est adapté pour la grande précision.
Lorsque de longs déplacements d’axe doivent s’effectuer à grande vitesse avec des accélérations importantes : il est clair que ces déplacements se font outils hors matière d’un usinage à un autre, à l’intérieur de la matière, la vitesse est de toute façon limitée par la résistance de l’outil. On est la dans des préoccupations de productivité, gagner quelques minutes pour chaque pièce afin de gagner suffisamment pour justifier l’investissement au bout de quelques années, lorsque la machine est utilisée pour de la série toute la journée.
Lorsqu’il y a plusieurs pièces à usiner dans une grande plaque, l’investissement dans un logiciel d’imbrication (nesting) permet d’optimiser l’ordre des usinages et limiter les déplacements d’outil.
Si les déplacements hors usinage ne sont pas trop longs, le gain de productivité entre les servo moteur et les moteurs pas à pas avec codeur de forte puissance ne sera pas important.
Principe de l’asservissement
Le principe de base de l’asservissement est de mesurer, en permanence, l’écart entre la valeur réelle mesurée du processus asservi et la valeur de consigne que l’on désire atteindre, puis de calculer la commande appropriée à appliquer à un (ou des) actionneur(s) de façon à réduire cet écart le plus rapidement possible.
Pour l’asservissement, la consigne évolue en permanence, ce qui n’est pas le cas de la régulation ou la consigne reste stable (exemple d’une régulation de chauffage)
A ) Qualités de l’asservissement
La précision
C’est la capacité du système à se rapprocher le plus possible de la valeur de consigne.
La rapidité
C’est la capacité du système à atteindre dans les meilleurs délais son régime stable.
La stabilité
C’est la capacité du système à se rapprocher de la consigne avec le minimum d’oscillation.
Le taux de dépassement caractérise l’amplitude maximale des oscillations.
B ) Les correcteurs
Un correcteur est un algorithme de calcul qui délivre un signal de commande à partir de la
différence entre la consigne et la mesure.
Le correcteur PID agit de 3 manières :
Action Proportionnelle : l’erreur est multipliée par un gain G appelé aussi Kp
Action Intégrale : l’erreur est intégrée et divisée par un gain Ti appelé aussi Ki
Action Dérivée : l’erreur est dérivée et multipliée par un gain Td appelé aussi Kd
Pour ces trois paramètres, le réglage au-delà d’un seuil trop élevé a pour effet d’engendrer une oscillation du système de plus en plus importante menant à l’instabilité.
L’analyse du système avec un PID est très simple, mais sa conception peut être délicate, voire difficile, car il n’existe pas de méthode unique pour résoudre ce problème.
Il faut trouver des compromis, le régulateur idéal n’existe pas
L’action proportionnelle : lorsque P augmente, le temps de montée (rise time) est plus court, mais il y a un dépassement plus important. Le temps d’établissement varie peu et l’erreur statique se trouve améliorée.
L’action intégrale : Lorsque 1/Ti augmente, le temps de montée est plus court, mais il y a un dépassement plus important.
Le temps d’établissement au régime stationnaire s’allonge, mais dans ce cas on assure une erreur statique nulle.
Donc plus ce paramètre est élevé, plus la réponse du système est ralentie.
L’action dérivée : lorsqu’augmenté, le temps de montée change peu, mais le dépassement diminue.
Le temps d’établissement au régime stationnaire est meilleur. Pas d’influences sur l’erreur statique.
Si ce paramètre est trop élevé dans un premier temps il stabilise le système en le ralentissant trop, mais dans un deuxième temps le régulateur anticipe trop
et un système à temps mort élevé devient rapidement instable.
Simulateur PID en ligne : http://www.olliw.eu/storm32bgc-wiki/PID_online_simulator
Un facteur externe a l’électronique de commande et aux servo moteur car dépendant de la structure mécanique de chaque machine est celui de l’inertie.
Trouver la bonne formule de PID en précision, stabilité et rapidité en fonction de l’inertie est très délicat à régler manuellement.
Les servo moteurs ont des liaisons série ( modbus, CAN, Ethernet … ) permettant de les paramétrer via un logiciel, ils ont généralement un mode auto-tuning (auto-réglage).
Libre à vous de modifier ensuite les gains manuellement si vous les désirez.
Ci-dessous un exemple d’écran auto-tuning d’un logiciel de paramétrage servo
Certains servo moteurs possèdent un frein, cela permet de maintenir une position lorsque l’électricité est coupée, très utile notamment pour l’axe Z lorsque l’électricité est coupée.
Motorisation des axes avec des moteur pas à pas
Motorisation des axes avec des moteur pas à pas
Le moteur pas à pas fut inventé en 1936 par Marius Lavet, un ingénieur français des Arts et Métiers, pour l’industrie horlogère (source Wikipédia)
I ) Fonctionnement
Le moteur pas-à-pas possède un rotor avec un aimant permanent et un stator avec deux bobines A et B, le courant traverse ces bobines dans un sens puis ensuite dans l’autre inversant ainsi les polarités.
L’extérieur du rotor ainsi que les noyaux des bobines du stator ont des dents.
La construction est réalisée pour que lorsque les dents de la bobine A aimantent les dents du pôle opposé du rotor, les dents de la bobine B ne soient en face d’aucune dent du rotor.
Ainsi lorsque c’est la bobine B qui est alimentée a son tour, le rotor fait une légère rotation, l’aimantation alignant ces autres dents.
Les possibilités de déplacement angulaire
sont nombreuses, selon le sens de déplacement du courant dans les bobines,
on attire différentes dents du rotor (dents rouges ou bleus dans cette animation)
Il y a beaucoup de types de moteurs, pas à pas.
Ceux utilisés par les machines CNC sont précisément des moteurs pas-à-pas hybrides bipolaires.
Si vous démontez un moteur pas à pas vous verrez 8 enroulements dans le stator, même s’il y a bien que deux bobines en deux parties réparties sur tout le pourtour.
Il y a d’ailleurs 4 fils correspondant aux 2 extrémités d’une bobine plus 2 extrémités de l’autre bobine.
Remarques : ne démontez pas des moteurs pas-à-pas que vous comptez utiliser, après démontage, la qualité des aimants permanents à l’intérieur est diminuée et le moteur sera moins performant après remontage.
II ) Normes et caractéristiques
La norme Nema correspond à des dimensions utiles pour la fixation du moteur dans une machine.
Ce qui permet l’interopérabilité puisqu’un moteur Nema 23 d’un fabricant peut être remplacé par un autre moteur nema 23 de mêmes caractéristiques d’un autre fabricant.
Contrairement à ce que beaucoup pensent, Nema n’indique rien sur la puissance du moteur, il est vrai que plus un moteur est gros plus il y a de chance qu’il soit puissant, mais la taille c’est aussi la longueur du moteur. Et un moteur Nema 17 long peut être plus puissant qu’un Nema 23 très court.
Les moteurs pas-à-pas plus longs ont des bobines de stators plus importantes, les rotors ont le double d’aimants permanents 4 au lieu de 2, ce qui augmente la puissance.
Ce qui compte dans un moteur pas à pas c’est le couple en N. m, c’est indiqué sur les fiches techniques du fabricant.
Le couple disponible peut être différent selon la vitesse de rotation du moteur et l’intensité du courant envoyé dans ses bobines.
Le couple indiqué par le fabricant est celui du « couple d’arrêts », le couple maxi à partir du moment où on fait sauter un pas le moteur à l’arrêt.
Le couple ensuite diminue en fonction de la vitesse, un moteur pas à pas est plus performant à faible vitesse qu’à vitesse importante.
Le couple possible sans perte de pas est plus faible au moment du démarrage qu’en vitesse de travail, c’est pour cela que pour le pilotage des moteurs pas à pas il faut paramétrer des phases d’accélération et décélérations.
Il est évident que plus un moteur est gros, plus ses bobinages pourront supporter une intensité importante et plus il pourra maintenir un couple important à haute vitesse.
Mais pour un même moteur plus on l’alimente avec un voltage important, plus il gardera du couple à grande vitesse, il est également évident que les moteurs de plus grande taille acceptent des voltages plus élevés que les petits. Dans les données constructeur il y a une plage pour alimenter les moteurs pas à pas, par exemple 12V à 50V, choisissez toujours la partie haute de la plage par exemple une alimentation électrique de 36V au lieu de 24V ou mieux 48 V.
Le moteur pas-à-pas bipolaire classique permet de faire 200 pas en un tour c’est-à-dire à chaque fois des déplacements angulaires de 1,8 deg
On peut trouver également des moteurs PAP de 400 pas / tours avec des déplacements angulaires de 0,9 deg
III ) Branchements
Les pilotes de moteurs pas-à-pas ont un bornier où doivent être branchés les 4 fils du moteur.
Cet emplacement est noté A+ A – (une bobine du moteur) et B+ B – (l’autre bobine du moteur)
Souvent les moteurs bipolaires ont comme couleur de fils rouge, bleu, vert, noir correspondant à A+ A — B+ B-
Sinon cela peut être marron, orange, rouge et jaune pour A+ A — B+ B —
Mais vous pouvez très bien tomber sur un code de couleur de fils plus exotique, il donc nécessaire de connaître la méthode ci-dessous qui consiste a tester les bobines avec un testeur de continuité.
Pour brancher correctement les fils, il faut faire un test de continuité entre ceux-ci pour voir s’ils appartiennent à la même bobine ou pas.
Si vous identifiez une bobine, car les deux fils font sonner le testeur de continuité appelez la B ou A cela n’a pas d’importante, si vous l’appelez arbitrairement, A l’autre s’appellera B.
Maintenant que l’une des bobines a été nommée A lequel fil de la bobine est A+ lequel est A — ? cela n’a pas beaucoup d’importance non plus, si les fils sont inversés le moteur tournera à l’envers.
Pour faire tourner un moteur pas à pas dans l’autre sens, il faut inverser le branchement des fils d’une seule bobine, ou changer un paramètre dans l’électronique de commande pour faire une inversion logicielle.
Vous saurez si le moteur tourne à l’endroit ou à l’envers quand vous ferez vos premiers tests de déplacement des axes de la machine.
Motorisation de la broche
Motorisation de la broche
La fonction d’une broche de machine outil est d’assurer un guidage précis en rotation de l’outil.
Cet outil est inséré dans un porte outil, la broche pour assurer le guidage en rotation possède des roulements.
I ) Motorisation de la broche
Pour certaines machines l’entrainement de la broche est assuré par un moteur grâce à une courroie.
Comme dans l’exemple ci-dessous pour une fraiseuse verticale.
Dans d’autre cas plus rares le moteur entraine directement la broche en bout avec un accouplement.
Pour une machine-outil il est essentiel d’avoir un réglage de vitesse de broche, les moteurs asynchrones devront donc avoir un variateur, par exemple un variateur par changement de fréquence.
Remarque :
Concernant les solutions de motorisation ci-dessus, l’ensemble pèse lourd.
Cela ne gène pas pour les fraiseuses verticales ( tête fixe ou déplacement seulement en Z ) mais pose problème pour les fraiseuses à portique.
Pour les fraiseuses à portique, on va privilégier les électrobroches ( motorisation et guidage compact dans un même ensemble ) ou les broches VFD ( variation de fréquence )
II ) Les électrobroches
Cette fois le guidage et l’entrainement en rotation sont regroupé dans un même matériel.
Le moteurs électrique universel, c’est le type de moteur qu’on trouve partout dans le matériel électroportatif, les appareils électroménager …
Le moteur électrique universel à beaucoup d’éléments communs avec le moteur à courant continu, notamment un collecteur et des balais.
Par contre même si dans la pratique on branche ce type de moteur sur une prise électrique secteur, donc 220V monophasé, on peut faire fonctionner indifféremment le moteur universel en continu ou alternatif.
Le moteur universel est très utilisé pour les puissances faibles à moyenne, il est économique à construire et à un bon couple au démarrage.
Par contre son principal inconvénient est qu’il nécessite un changement de balais au bout d’un certain temps à cause du frottement sur le collecteur.
Les étincelles entre les balais et le collecteur peuvent provoquer des perturbations électromagnétiques.
Les moteurs de fraisage doivent avoir des protections contre ces perturbations qui pourrait provoquer des déconnexions dans l’électronique de pilotage.
A ) Electrobroche avec moteur universel d’entrée de gamme
Il est possible d’adapter à des fraiseuses CNC des électrobroches prévus au départ pour des défonceuses.
Comme pour les modèles ci-dessus (Makita RT0701C, Bosh Colt et Dewalt DWP611 ) qui sont assez souvent utilisés pour le fraisages avec des petites fraiseuses Hobbyistes.
Ces défonceuses ont en général une puissance de 800W, elles sont plus bruyantes que les broches dédiés au fraisage et il est préférable de les réserver à l’usinage du bois et matières plastiques. Les roulements supporteraient mal des usinages réguliers et prolongés par exemple dans l’aluminium.
B ) Electrobroche avec moteur universel de milieu de gamme.
Ces électrobroches sont construites spécifiquement pour l’usinage. Elle peuvent usiner le bois les matières plastiques et les métaux tendres ( aluminium, cuivre, laiton … )
La puissance va de 800W à 1050W et des options sont possibles pour avoir
– un système de changement automatique d’outils ATC ( Automatic Change Tools )
– un pilotage de la vitesse à partir de l’électronique de commande
Les broches de marque Allemande Kress rachetés récemment par une autre marque Allemande AMB sont très connus et équipent beaucoup de fraiseuses CNC.
Ont trouve également dans la même gamme la marque Allemande Mafell.
C ) Electrobroches avec moteur universel puissantes
Les électrobroches Suisse Suhner peuvent aller jusqu’a une puissance de 1800 Watt.
Les porte outils sont identiques et compatibles avec les broches Kress AMD et Mafell
Le même système de changement automatique d’outil que les broches Kress peut être utilisé.
Mais contrairement au moteur à courant continu classique, la partie bobinée ( inducteur ) est fixe.
Cette partie fixe bobinée est alimentée par un circuit électronique de commande qui va activer successivement les bobines, ont a donc plus les inconvénients du collecteur et des balais.
Ce sont des petits capteurs à effet Hall qui vont donner l’information à l’électronique pour commuter au bon moment.
Ci dessous le principe de fonctionnement
Les marques de matériel électroportatif sur batterie, passent progressivement du moteur électrique universel au moteur brushless.
II ) Branchement des électrobroche avec variateur de fréquence
Les prises XLR Aviation des électrobroches ont les connecteurs numérotés de 1 à 4
Il est important de relier la broche 4 à la terre. Pour les broches 123 une inversion va juste faire tourner la broche à l’envers.
III ) Exemple de l’inverter VFD Huanyang HY01D523B
Les inverteurs de l’entreprise Hongkongaise Huanyang sont bon marchés et très répandus, le modèle HY01D523B à une puissance de 1.5Kw.
Il est important que la carcasse de la broche soit reliée à la terre, généralement elle est reliée à terre par l’intermédiaire du support de broche lorsque la machine elle même est reliée à la terre.
Pour un pilotage manuel de la broche seul le bornier inférieur est utilisé, les borniers verts supérieurs sont à relier à un panneau de commande ou l’interpolateur de pilotage.
Paramétrage de l’inverter VFD Huanyang HY01D523B
A faire dans cet ordre
Pd013 —-> réinitialisation de l’appareil mettre 1 ( paramètre 8 sur certains modèles plus anciens )
Pd005 —-> fréquence maximale, entrer 400 (soit 24000 rpm)
Pd004 —–> fréquence nominale du moteur, entrer 400
Pd003 —–> fréquence de démarrage, c’est à dire fréquence à laquelle le moteur va se lancer lors du démarrage avec le bouton run.
mettre par exemple 200, soit 12000 tours…
Pd011 ——> fréquence minimale. Par exemple 50 soit 3000 tours : en dessous le moteur à trop peu de couple pour usiner… Par contre si on veux se servir d’une pinule, il est possible de choisir encore plus lent.
Pd014 —> temps pour accélérer, en secondes, sur une 1kw5 normalement 2 secondes suffisent
Pd015 —-> temps pour s’arrêter (on ne se servira pas de la fonction de freinage qui abime le matériel, ici comme on est pas pressé on va laisser la broche s’arrêter en douceur, et on rentre 2 ou 3 secondes également)
Pd023 —-> Si 1 le moteur peut tourner dans 2 sens / si 0 le moteur tourne dans un seul sens
Pd144 —-> vitesse du moteur à 50hz, entrer 3000 au lieu de 1440 (ceci ne change pas le comportement du variateur, c’est juste pour avoir un affichage de la vitesse qui correspond à la réalité)
Pd145 —-> le variateur va augmenter la tension s’il détecte que le moteur peine. Ce paramètre peut être réglé de 1 à 10. Attention: plus c’est haut, plus le moteur risque de chauffer en cas d’effort important. On peut rentrer 6 par exemple pour ne pas faire trop chauffer le moteur.
III ) Les broches dont la vitesse de rotation varie avec la fréquence
Les moteurs triphasés asynchrones sont prévus pour tourner à 3000 tr/min avec 50 Hz (fréquence du réseau électrique français)
Si on transporte les mêmes moteurs aux États-Unis, ils tourneront à 3600 tr/min avec 60 Hz
La vitesse du moteur triphasé asynchrone dépend de la fréquence d’alimentation de ses bobines.
Le principe est donc de lisser le signal alternatif du réseau électrique (courant continu) puis avec une électronique de puissance, recréer un signal alternatif dont la fréquence cette fois-ci peut varier selon le choix de l’utilisateur.
Ce type de variateur peut être utilisé pour faire varier n’importe quel moteur asynchrone triphasé 220 ou 380 V même si chez vous, vous n’avez que du 220 V ou 240 V mono.
Ceci est très pratique pour faire fonctionner une machine en 380V triphasé lorsque l’on dispose que d’un réseau 220V monophasé.
Il existe également des variateurs VFD triphasé —-> triphasé
La liaison entre le variateur et la broche doit se faire via un câble blindé, la connexion se fait avec un connecteur XLR type aviation
Les trois phases UVW se branchent respectivement sur les broches 123 du connecteur XLR.
La terre n’est pas toujours connectée à la broche N° 4, s’il y a un défaut d’isolement dans la broche au niveau de sa carcasse, l’électricité pourra toujours partir vers la terre de la machine via le support de broche, il est donc important de mettre le chassis de la machine à la terre.
La motorisation
Les systèmes d’entrainement
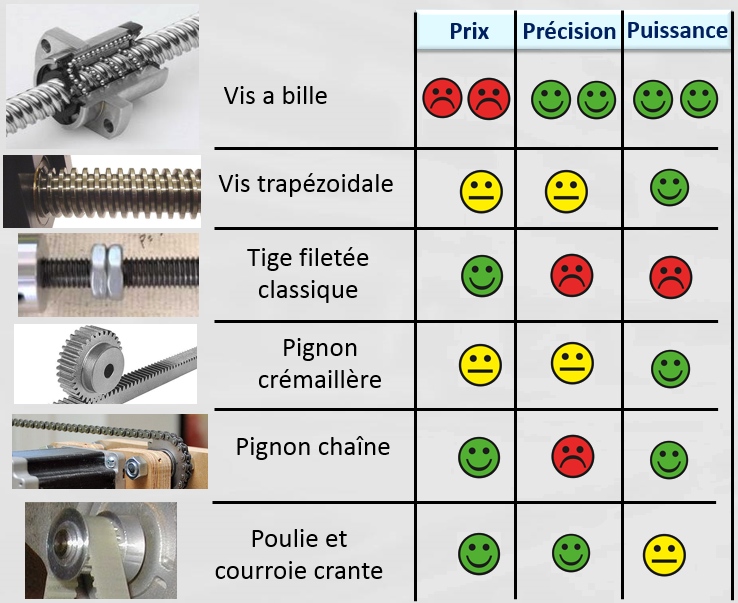
Système d’entrainement par pignon crémaillère
Avantages :
- Permet des vitesses de déplacement et accélérations importantes
- Peut transmettre des charges importantes sur de longues distances
- Moins cher que les vis à billes en particulier sur les longues distances
- Garde la mêmes précision quel que soit la distance de déplacement
Inconvénients :
- Nécessite un système permettant d’annuler les jeux dans le cas des pignons à denture droite.
Il est préférable pour limiter les jeux de fonctionnement d’utiliser des crémaillères et pignons à dentures hélicoïdales. - Ce système reste cependant moins précis que les vis à bille mais comme les machines de grande taille ne sont pas faites pour usiner le micron la précision reste suffisante.
Système d’entrainement par courroies crantées
Avantages :
- Permet des vitesses de déplacement et accélérations importantes
- Grande précision et pas de jeux de fonctionnement
- Solution très économique
- Fonctionnement silencieux
Inconvénients :
- Ne permet pas de transmettre des efforts aussi important qu’avec une vis à bille
- Perd en précision (allongement) sur des longues distances contrairement aux crémaillères.
Remarques : ces inconvénients peuvent être réduis en choisissant des courroies crantées renforcées avec fil d’acier, un système avec courroies crantés qui s’engrène avec une autre cette fois fixe permet également de supprimer l’allongement sur les grandes distances mais le système est très difficile à mettre en oeuvre.
Les systèmes d’entrainement
Le choix du système de transmission pour une CNC dépend de beaucoup de paramètres
– du budget
– de la précision requise
– du couple à transmettre
– des vitesses et accélération de déplacement
Le système doit également être cohérent avec les reste de la machine, pas la peine de choisir une transmission très chère et ultra précise si le châssis de la machine n’est pas suffisamment rigide.
Remarques :
Les transmissions par chaines ou vis écrous classiques ne sont pas détaillés ici car ils présentent trop d’inconvénients pour la construction de fraiseuses CNC.
La transmission ne doit pas être considérée seule, les avantages et inconvénients d’une solution peuvent être modulés en fonction de la rigidité de la machine, de la motorisation utilisée.
Système d’entrainement par vis à billes
Avantages :
Très grande précision, pas de jeux, pas de frottements dans la transmission
Inconvénients :
Prix en particulier lors des grandes longueurs.
Ne conviens pas aux transmissions de très grandes longueurs, risque de flambage lorsque la vitesse de rotation augmente et dans ce cas il est préférable d’entrainer en rotation l’écrou plutôt que la vis.
Remarques : des nouvelles techniques de fabrication ont réduit le prix des vis à billes, il y a plusieurs niveaux de précision dans les vis à billes donc différents prix.
Système d’entrainement par vis écrous à profil trapézoidal ou carré.
Avantages :
- Permet de transmettre des efforts importants
- Solution plus économique que les vis à bille
Inconvénients :
IL y a beaucoup de jeu entre la vis et l’écrou qu’il faut compenser pour l’éliminer avec un ressort (ce n’est pas une solution idéale)
Ces vis trapézoïdales sont utilisées habituellement pour des déplacements avec des efforts importants sans nécessiter de précisions.
Les vis à filet trapézoïdal ou carré ne sont pas adaptées aux déplacements d’axe pour la plupart des machines CNC,
à cause du jeu et donc du manque de précision lorsque les déplacements changent de direction.
On trouve cependant ce type de transmission pour de petites fraiseuses CNC bon marché pour des raisons de coûts.
Structure d’une CNC
[:fr]
Structure d’une CNC
Sur le web
Protocase https://www.protocase.com/
Entreprise Canadienne de création de carters, boitiers métalliques pour prototypage.
Logiciel Protocase Designer pour créer sa forme en tôle et directement un devis
Les options et accessoires
Les options et accessoires
du stratifié carbone sans faire de poussière, de la pièrre, du marbre …
Concernant le modèle ci-dessus, la table en aluminium rainuré à une surface de bridage de 345 x 305mm
Le système rend l’usinage plus silencieux et grâce à la pompe de transfert intégré, le liquide peut être rapidement évacué après l’usinage de la pièce.
Le liquide de refroidissement est à base de Glycol, bien connu dans l’industrie automobile pour ses propriétés réfrigérantes et non corrosives.
En Anglais A.T.C ( Automatic Tool Changer )
Les systèmes de guidage
Les systèmes de guidage
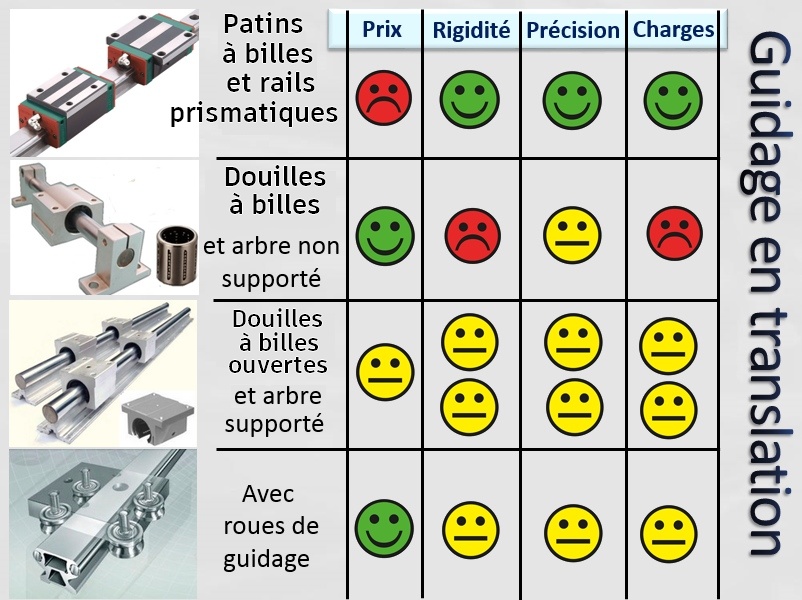
Le choix du système de guidage en translation pour une CNC dépend de beaucoup de paramètres.
– du budget
– de la précision requise
– des efforts à supporter
– de la structure de la machine
Le système de guidage doit être normalement cohérent avec le reste de la machine et un type de guidage correspond généralement à un type de châssis.
Vous avez ci-dessous un contre exemple avec une fraiseuse 6040 qu’on peut trouver commercialisée avec trois types de guidages, bien que la rigidité de la structure est pratiquement identique dans les trois cas.
La raison est économique, des rails prismatique coûtent plus cher que des rails cylindriques.
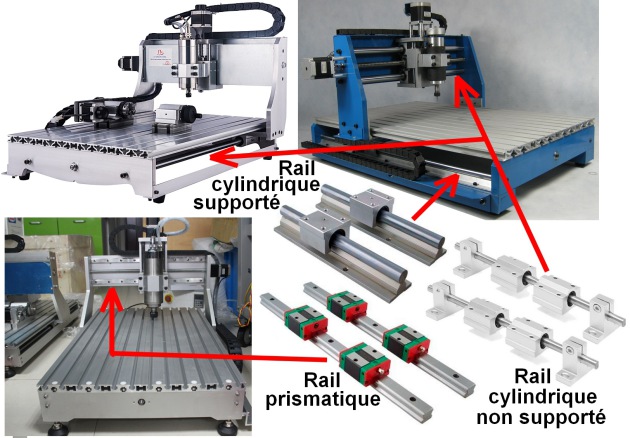
Si votre machine possède des rails assez long non supportés, il est impossible d’usiner des matières dures telles que bois massif et aluminium, d’importantes vibrations se feront au niveau du rail.
Les rails supportés peuvent être cylindriques ou prismatiques, le choix entre les deux doit se faire en fonction :
– de la sollicitation de la machine, si vous utiliser la machine toute la journée avec des cadences industrielles, les rails prismatiques en général vont être moins usés que les cylindriques au bout de plusieurs dizaines d’années.
– de la précision recherchée, les patins prismatiques peuvent être pré-contrains, donc absence totale de jeux de fonctionnement. Mais si le reste de la machine fait que vous avez des pertes de précision ailleurs, rails cylindriques ou prismatiques vous ne verrez pas la différence au niveau précision, surtout si c’est pour usiner du bois.
– de la charge à supporter, si vous avez un portique de machine très lourd, les guidages cylindriques se font que sur une seule rangée de bille alors que pour les patins prismatiques cela peut être sur plusieurs rangées.
Les axes d’une fraiseuse CNC
Les axes d’une fraiseuse CNC
Fraiseuse 3 axes
Les 3 axes sont les axes de translation nommés XYZ
L’axe de la broche Z n’est pas forcément perpendiculaire à la table
Dans le cas des machines à banc fixe ( la table se déplace ) on trouve des fraiseuses verticales et horizontales.
Pour les fraiseuses verticales : l’axe de la broche est perpendiculaire à la table
Pour les fraiseuses horizontales : l’axe de la broche est parallèle à la table
Exemple des fraiseuses CNC Formosa
Les fraiseuses Formosa sont des fraiseuses à portique et pour ce type de machine l’axe Z est perpendiculaire à la table.
Remarque : il existe une convention dans le monde industriel ou l’axe X est plutôt celui du plus grand déplacement.
Cette convention n’est pas forcément respectée pour les machines autoconstruites.
De façon que quelle que soit la taille de la machine l’interface logicielle soit la même.
La majorité des fraiseuses à commande numérique sont des machines 3 axes.
Ce qu’il est possible de faire avec une fraiseuse 3 axes |
Ce qu’il est impossible de faire avec une fraiseuse 3 axes |
|
|
Les fraiseuses permettant l’usinage multi-axes
On parle d’usinage multi-axes quand la machines dispose d’au moins 4 axes de mouvement. En général, les machines multi-axes ont des axes XYZ pour effectuer des mouvements de translation, ainsi qu’un ou plusieurs axes capables d’effectuer des rotations.
L’ajout d’axes supplémentaires ouvre la possibilité de réaliser des usinages compliqués et impossibles à faire avec des machines 3 axes en translation ; cependant les machines multi-axes sont également plus chères, et plus complexes à utiliser.
Le nombre d’axes peut aller de 4 à plus de 10, et bien entendu plus la machine dispose d’axes plus son prix est élevé.
Fraiseuse 4 axes
En général, une fraiseuse 4 axes est tout simplement une fraiseuse 3 axes dotée d’un plateau tournant (le plus souvent parallèle à l’axe X ou Y de la machine).
C’est sur ce plateau tournant que va être fixée la matière à usiner, l’outil de coupe peut ainsi travailler sur toutes les faces parallèles à l’axe de rotation sans que l’opérateur doive intervenir pour retourner la matière le 4ème axe se charge de cela au fur et à mesure selon les commandes du programme.
Le 4ème axe est utilisé soit en mode « indexation », soit en mode « continu ».
En mode indexation, la broche avec la fraise est désactivée et aucune coupe n’est faite jusqu’à ce que l’axe 4 achève son mouvement de rotation.
En mode continu par contre, l’outil de coupe travaille en même temps que l’axe 4 tourne.
Le mode continu permet de faire des sculptures sur des objets cylindriques, des torsades ect …
Fraiseuse 5 axes
On peut trouver sous cette catégorie plusieurs topologies de construction.
Une fraiseuse 5 axes comporte toujours 3 axes linéaires (X, Y, Z) et 2 axes rotatifs à choisir parmi A, B et C.
Les machines vont se différencier par la position des axes rotatifs.
On trouve principalement 2 types de fraiseuse 5 axes :
2 axes rotatifs sur tête (souvent axes rotatifs B et C )
Avantage des axes rotatifs sur tête : permet d’usiner sur 3 plans sans démontage, des pièces volumineuses ou lourdes
Inconvénient : moins de rigidité et de puissance que pour des axes rotatifs sur table
Dans le domaine des fraiseuses 5 axes non industriels on trouve par exemple la fraiseuse 5 axismaker.